Leak Testing [LT]
Leak Testing refers to the process of observing the leaks in a vessel or structure in order to identify defects in it. It tests manufactured parts to make sure fluids can’t leak into or out of the part. There are several different Leak Testing technologies.
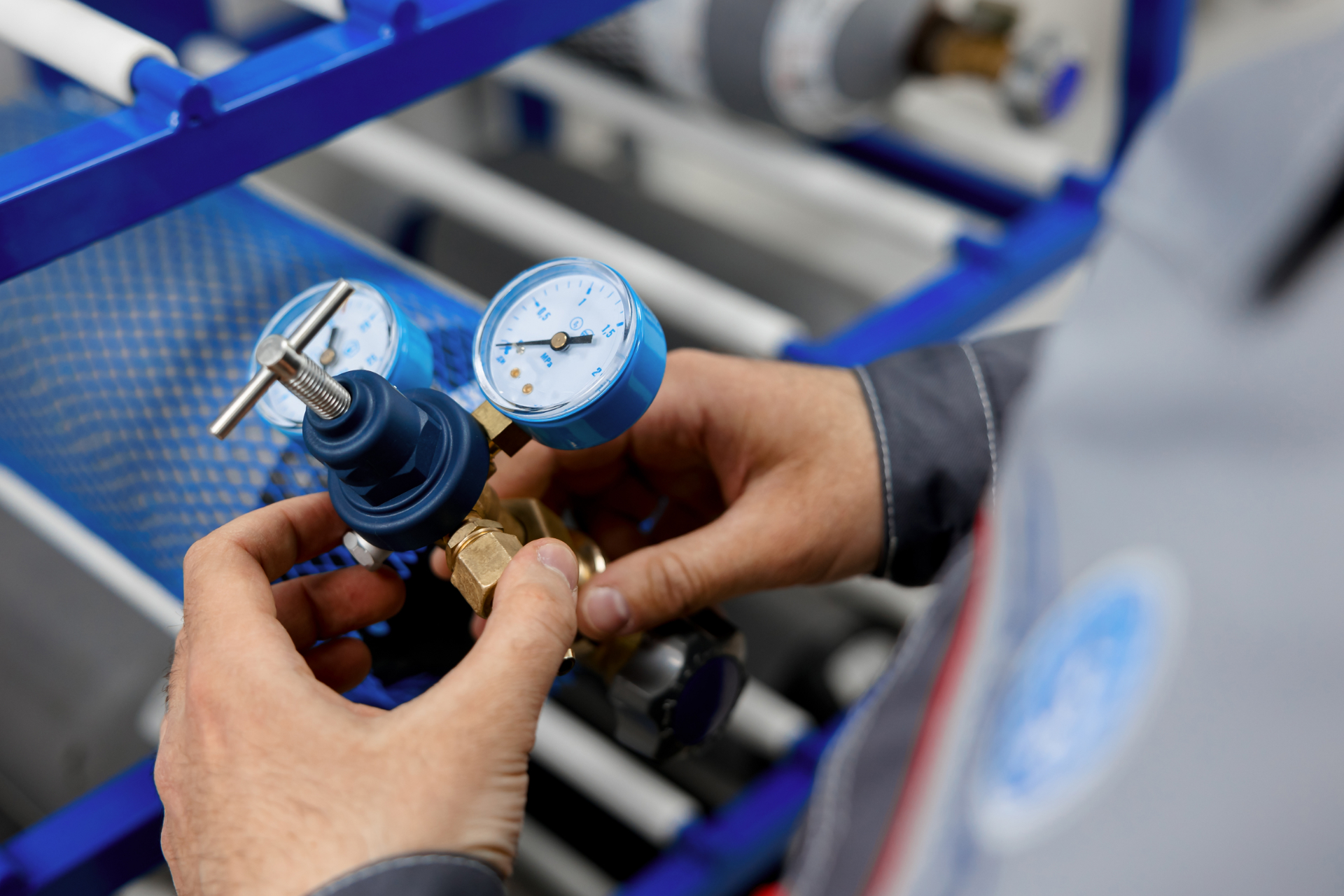
The methods used vary from simple bubble testing combined with a visual inspection, to very sensitive methods using radioactive gases. Inspectors can detect leaks within a vessel using measurements taken with a pressure gauge, or electronic listening devices, among others. Three of the most commonly used types are:
- Pressurised Fluid
- Pressurised Air/Gas
- Vacuum
Pressurised Fluid, where leaks are detected visibly or through measured decay by specialised fluid pressure gauges or electronic sensors:
• simulates real-world conditions for parts designed to contain or pass fluid.
• performs superbly for testing at pressures above 500PSI.
• may be used for destructive testing (pressurise to burst).
Pressurised Air/Gas, where leaks are detected visibly when immersed in a fluid, or audibly when using sensitive “listening” devices or by electronic sensors when using pressure-decay instruments:
• is fast: as air molecules are roughly 500X smaller than water molecules. Can detect much smaller voids in parts in considerably less time than fluid testing.
• has low cost: sensitive equipment is available by many manufacturers at far lower costs than sensitive fluid systems.
• is clean: parts do not have to be cleaned of fluids after the test.
Vacuum, where leaks are detected visibly when immersed in a fluid (liquid entry into part) or by specialised electronic vacuum sensors or gauges with vacuum-decay instruments:
• is ideal for parts that will have an internal vacuum applied.
• can create leak paths that cannot be replicated by pressure testing such as dynamic seals (“o” rings and rubber diaphragm valves).
Pressurised Fluid
• Added Costs: parts often require cleaning/drying after test.
• Time Consuming: the time required for fluid to leak through a small void in the part can be considerable, sometimes hours.
• Messy: fluid gets everywhere when testing using this method.
• Costly Equipment: is often custom made per application
Pressurised Air/Gas
• Very costly to achieve pressures above 500PSI.
• As air compresses so much more than fluid, can be difficult to use for some destructive tests.
• Only represents (does not duplicate) “real-world” testing for parts containing or passing fluid.
Vacuum
• Not good for testing parts that would otherwise have pressure applied internally in actual application as the vacuum may inadvertently seal small voids in flexible parts.
• Vacuum is limited to approximately -14.7 PSI (ideal vacuum). With typical vacuum pumps, only -10 PSI or so may be possible.
Leak testing is typically used to detect small leaks in products including, but not limited to: valves, welds, manifolds, high purity piping, hydraulic lines, storage tanks, and more.
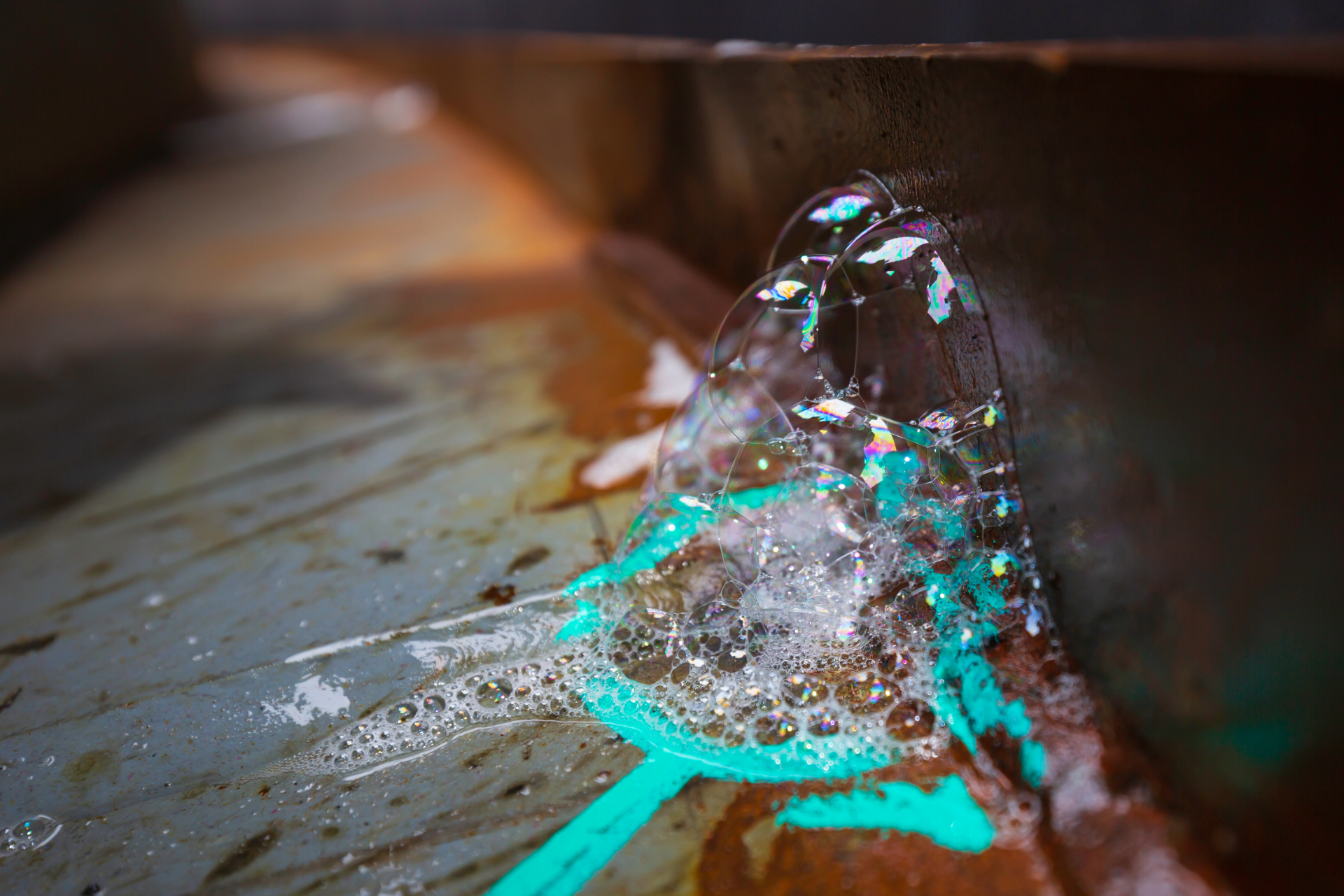
Newtron Leak Testing can be used to assess a wide array of assets in a range of industries like Oil and Gas, Automotive, Manufacturing, Maritime, Energy.
International Organization for Standardization (ISO)
ISO 10332 Non-destructive testing of steel tubes — Automated ultrasonic testing of seamless and welded (except submerged arc-welded) steel tubes for verification of hydraulic leak-tightness (2010)
ISO 20484 Non-destructive testing — Leak testing — Vocabulary (2017)
ISO 20486 Non-destructive testing — Leak testing — Calibration of reference leaks for gases (2017)
ISO 18081 Non-destructive testing — Acoustic emission testing (AT) — Leak detection by means of acoustic emission (2016)
ISO 20485 Non-destructive testing — Leak testing — Tracer gas method (2017)
ISO 27895 Vacuum technology — Valves — Leak test (2009)
ISO 16247 Road vehicles — Detection of exhaust system leaks — Helium test method and detection device specification (2004)
ISO/DIS 3459 Plastic piping systems — Mechanical joints between fittings and pressure pipes — Test method for leak tightness under negative pressure
ISO/DIS 13844 Plastics piping systems — Elastomeric-sealing-ring-type socket joints for use with plastic pressure pipes — Test method for leak tightness under negative pressure, angular deflection and deformation
ISO 12807 Safe transport of radioactive materials — Leakage testing on packages (2018)
ISO 29463-4 High-efficiency filters and filter media for removing particles in air — Part 4: Test method for determining leakage of filter elements-Scan method (2011)
ISO 15848-1 Industrial valves — Measurement, test and qualification procedures for fugitive emissions — Part 1: Classification system and qualification procedures for type testing of valves (2015)
ISO 16530-1 Petroleum and natural gas industries — Well integrity — Part 1: Life cycle governance (2017)
ISO 14644-7 Cleanrooms and associated controlled environments — Part 7: Separative devices (clean air hoods, gloveboxes, isolators and mini-environments) (2004)
ISO 13628-7 Petroleum and natural gas industries — Design and operation of subsea production systems — Part 7: Completion/workover riser systems (2005)
American Society for Testing and Materials (ASTM)
ASTM E1003-13(2018) Standard Practice for Hydrostatic Leak Testing, ASTM International, West Conshohocken, PA, 2018
American Society of Mechanical Engineers (ASME)
ASME Boiler and Pressure Vessel Code, Section V
This information is a collection of references. While we have made every attempt to ensure that information on this site is updated, Newtron is not responsible for any errors or omissions, or for the results obtained from the use of this information. It is not guaranteed to be complete, correct, current, or up to date and may be changed without prior notice.