Magnetic Particle Testing [MT]
Magnetic Particle Testing is a method used to identify surface or near-surface defects in a material by examining disruptions in the flow of the magnetic field within the material.
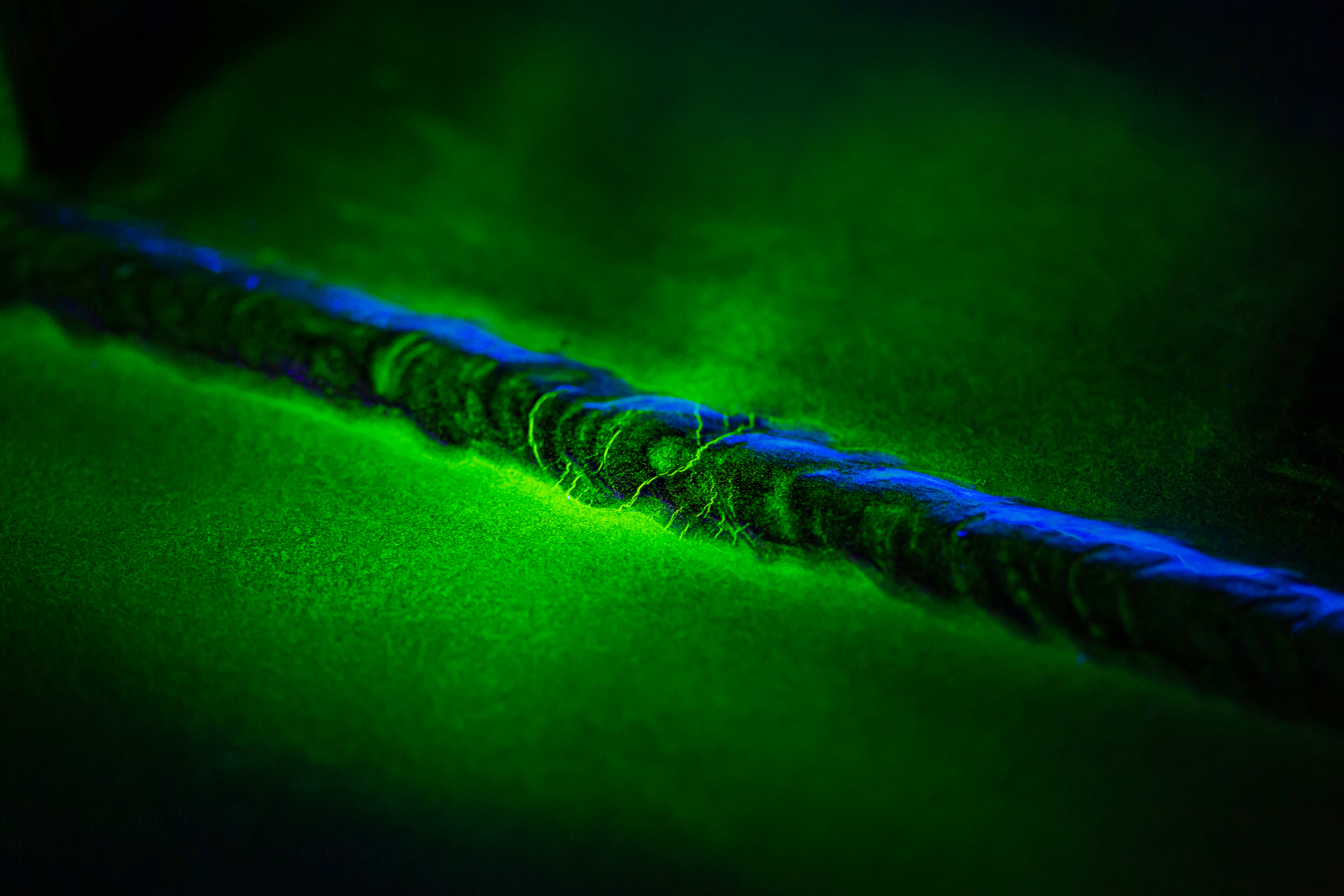
To use Magnetic Particle Testing, inspectors first induce a magnetic field in a material that is highly susceptible to magnetisation. After inducing the magnetic field, the surface of the material is covered with iron particles, which reveal disruptions in the flow of the magnetic field. These disruptions create visual indicators for the locations of imperfections within the material.
There are several advantages of MT that include but are not limited to:
- Detects both surface and near sub-surface defects
- Determines crack location
- Monitors crack length
- Identifies crack propagation modes
- Determines the cycles to crack initiation
- Provides immediate results
- It can detect defects that have been smeared over
- It can inspect parts with various geometries and materials (external splines, crankshafts, connecting rods, e.t.c.)
- Indications are visible to the inspector directly on the specimen surface
- The material tested must be ferromagnetic (e.g. steel, cast iron)
- Thick paint must be removed before inspection
- Post cleaning and post demagnetisation may be necessary
- Maximum depth sensitivity is typically quoted as 2.54 millimetres (may be deeper under perfect conditions)
- Inspector skills are important
Metals can be classified as ferromagnetic, paramagnetic, or diamagnetic. Ferromagnetic metals are those, which are strongly attracted to a magnet and can be easily magnetised, such as iron, nickel, and cobalt.
This NDT method can be used only on metals which can be easily magnetised, meaning ferromagnetic metals.
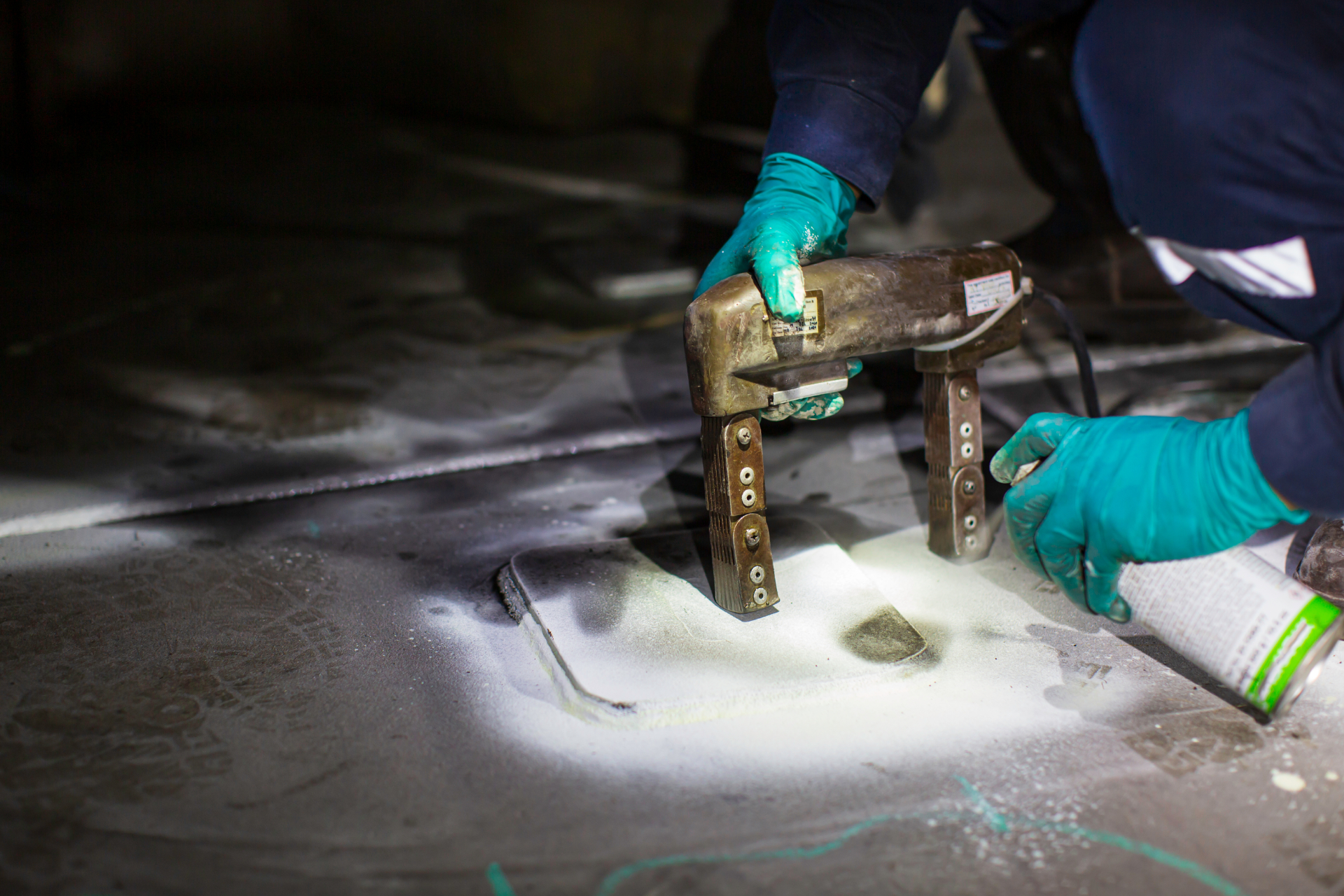
Newtron’s MP Testing services can be used to assess a wide array of assets: welds, castings, tools, bar-stock, and other components for quality control, surface integrity, and code conformance among others, in all industry sectors including petrochemical, structural steel, and power generation.
International Organization for Standardization (ISO)
ISO 3059 Non-destructive testing – Penetrant testing and magnetic particle testing – Viewing conditions
ISO 9934-1 Non-destructive testing – Magnetic particle testing – Part 1: General principles
ISO 9934-2 Non-destructive testing – Magnetic particle testing – Part 2: Detection media
ISO 9934-3 Non-destructive testing – Magnetic particle testing – Part 3: Equipment
ISO 10893-5 Non-destructive testing of steel tubes. Magnetic particle inspection of seamless and welded ferromagnetic steel tubes for the detection of surface imperfections
ISO 17638 Non-destructive testing of welds – Magnetic particle testing
ISO 23278 Non-destructive testing of welds – Magnetic particle testing of welds – Acceptance levels
American Society for Testing and Materials (ASTM)
ASTM E1444-05 Standard Practice for Magnetic Particle Testing
ASTM A 275/A 275M Test Method for Magnetic Particle Examination of Steel Forgings
ASTM A456 Specification for Magnetic Particle Inspection of Large Crankshaft Forgings
ASTM E543 Practice Standard Specification for Evaluating Agencies that Performing Nondestructive Testing
ASTM E 709 Guide for Magnetic Particle Testing Examination
ASTM E 1316 Terminology for Nondestructive Examinations
ASTM E 2297 Standard Guide for Use of UV-A and Visible Light Sources and Meters used in the Liquid Penetrant and Magnetic Particle Methods
American Society of Mechanical Engineers (ASME)
ASME Boiler and Pressure Vessel Code, Section V
This information is a collection of references. While we have made every attempt to ensure that information on this site is updated, Newtron is not responsible for any errors or omissions, or for the results obtained from the use of this information. It is not guaranteed to be complete, correct, current, or up to date and may be changed without prior notice.