Penetrant Testing [PT]
Penetrant Testing [PT] is a widely applied inspection method that utilises, most commonly, a dye to indicate material surface breaking discontinuities. It has many names, as it is also called Liquid Penetrant Inspection [LPI] or Dye Penetrant inspection [DP] in several industries but in simple words, it is a test for surface-breaking defects.
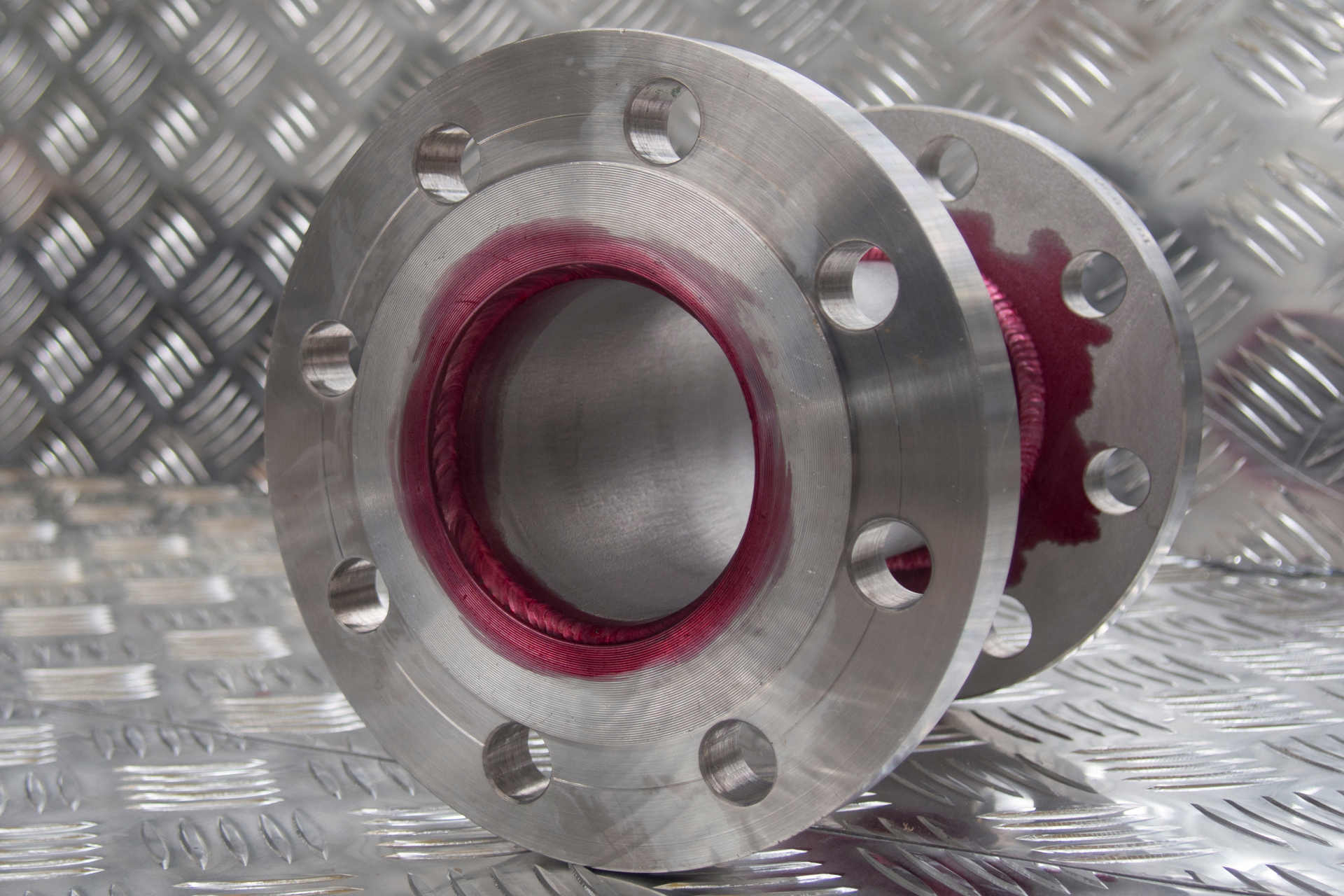
The principle of this testing method is that the liquid penetrant is drawn into the surface-breaking discontinuity e.g. cracks by capillary action and any excess surface penetrant is then, removed; a developer (typically a dry powder) is then applied to the surface, to draw out the penetrant in the discontinuity and produce a surface indication. It is a multi-step process: a) surface cleaning (degreasing e.t.c), b) application of a penetrant liquid (dipping, spray, brush), c) removal of excess penetrant (solvent, water), d) application of developer, e) inspection of test surface (visual, television camera), f) post-inspection cleaning (anti-corrosion solutions). Discontinuities as narrow as 150 nanometers can be detected. The indications produced are much broader than the actual flaw and are therefore more easily visible. Surface cleaning is a vital part of the Penetrant Testing technique.
There are several advantages of PT that include, but are not limited to:
- It works on complicated geometric shapes
- Penetrant Testing consumables are compact
- It is sensitive to small surface discontinuities
- Penetrant Testing materials are individually very cost-effective
- It provides visual results easy to size accurately
- It can only detect flaws on the surface.
- It only works on clean, smooth surfaces, which can make it unsuitable for some parts.
- There are environmental concerns linked to PT as it may require disposing of chemicals and expensive handling
- Visual contact with the test object is required
Penetrant Testing [PT] can be applied to any non-porous clean material (metals, plastics, or ceramics) but is unsuitable for dirty or very rough surfaces.
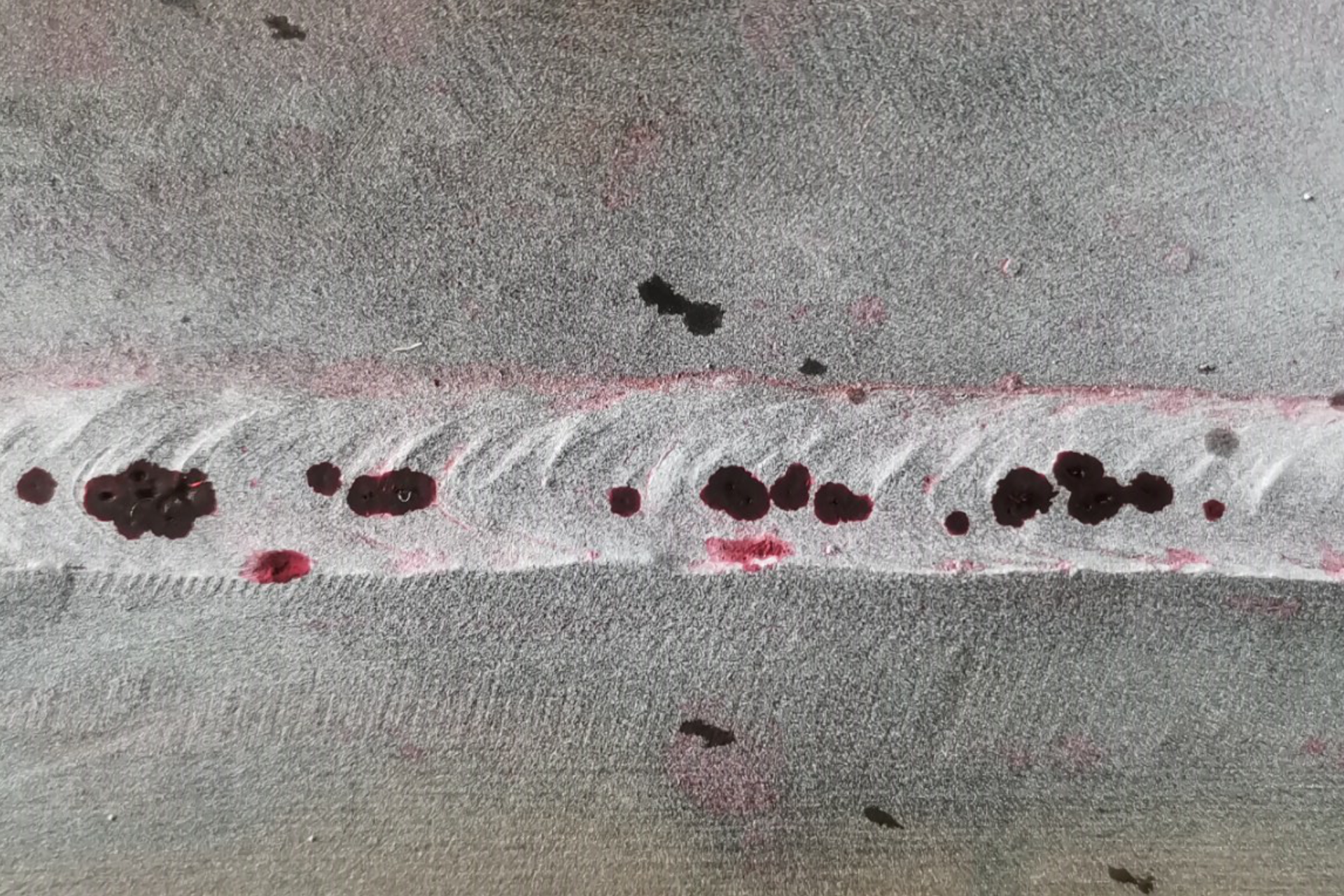
Newtron Technologies Penetrant Testing services are most commonly used in oil and gas, among other industries.
International Organization for Standardization (ISO)
ISO 3059 Non-destructive testing – Penetration testing and magnetic particle testing – Viewing conditions
ISO 3452-1 Non-destructive testing. Penetrant testing. Part 1. General principles
ISO 3452-2 Non-destructive testing – Penetrant testing – Part 2: Testing of penetrant materials
ISO 3452-3 Non-destructive testing – Penetrant testing – Part 3: Reference test blocks
ISO 3452-4 Non-destructive testing – Penetrant testing – Part 4: Equipment
ISO 3452-5 Non-destructive testing – Penetrant testing – Part 5: Penetrant testing at temperatures higher than 50 °C
ISO 3452-6 Non-destructive testing – Penetrant testing – Part 6: Penetrant testing at temperatures lower than 10 °C
ISO 10893-4 Non-destructive testing of steel tubes. Liquid penetrant inspection of seamless and welded steel tubes for the detection of surface imperfections.
ISO 12706 Non-destructive testing – Penetrant testing – Vocabulary
ISO 23277 Non-destructive testing of welds – Penetrant testing of welds – Acceptance levels
European Committee for Standardization (CEN)
EN 1371-1 Founding – Liquid penetrant inspection – Part 1: Sand, gravity die and low pressure die castings
EN 1371-2 Founding – Liquid penetrant inspection – Part 2: Investment castings
EN 2002-16 Aerospace series – Metallic materials; test methods – Part 16: Non-destructive testing, penetrant testing
EN 10228-2 Non-destructive testing of steel forgings – Part 2: Penetrant testing
American Society for Testing and Materials (ASTM)
ASTM E 165 Standard Practice for Liquid Penetrant Examination for General Industry
ASTM E 1417 Standard Practice for Liquid Penetrant Testing
American Society of Mechanical Engineers (ASME)
ASME Boiler and Pressure Vessel Code, Section V, Art. 6, Liquid Penetrant Examination
ASME Boiler and Pressure Vessel Code, Section V, Art. 24 Standard Test Method for Liquid Penetrant Examination SE-165 (identical with ASTM E-165)
This information is a collection of references. While we have made every attempt to ensure that information on this site is updated, Newtron is not responsible for any errors or omissions, or for the results obtained from the use of this information. It is not guaranteed to be complete, correct, current, or up to date and may be changed without prior notice.