Total Focusing Method [TFM]
The Total Focusing Method is an algorithm used as a means of leveraging data for better and more accurate readings. It is a processing method of using the data from Full Matrix Capture [FMC] – a strategy for collecting phased array data – to produce an image which is focused at every specified point.
TFM is using a similar approach to PAUT. Only, in this case, the focalization is applied everywhere in the region of interest, not only at a fixed depth.
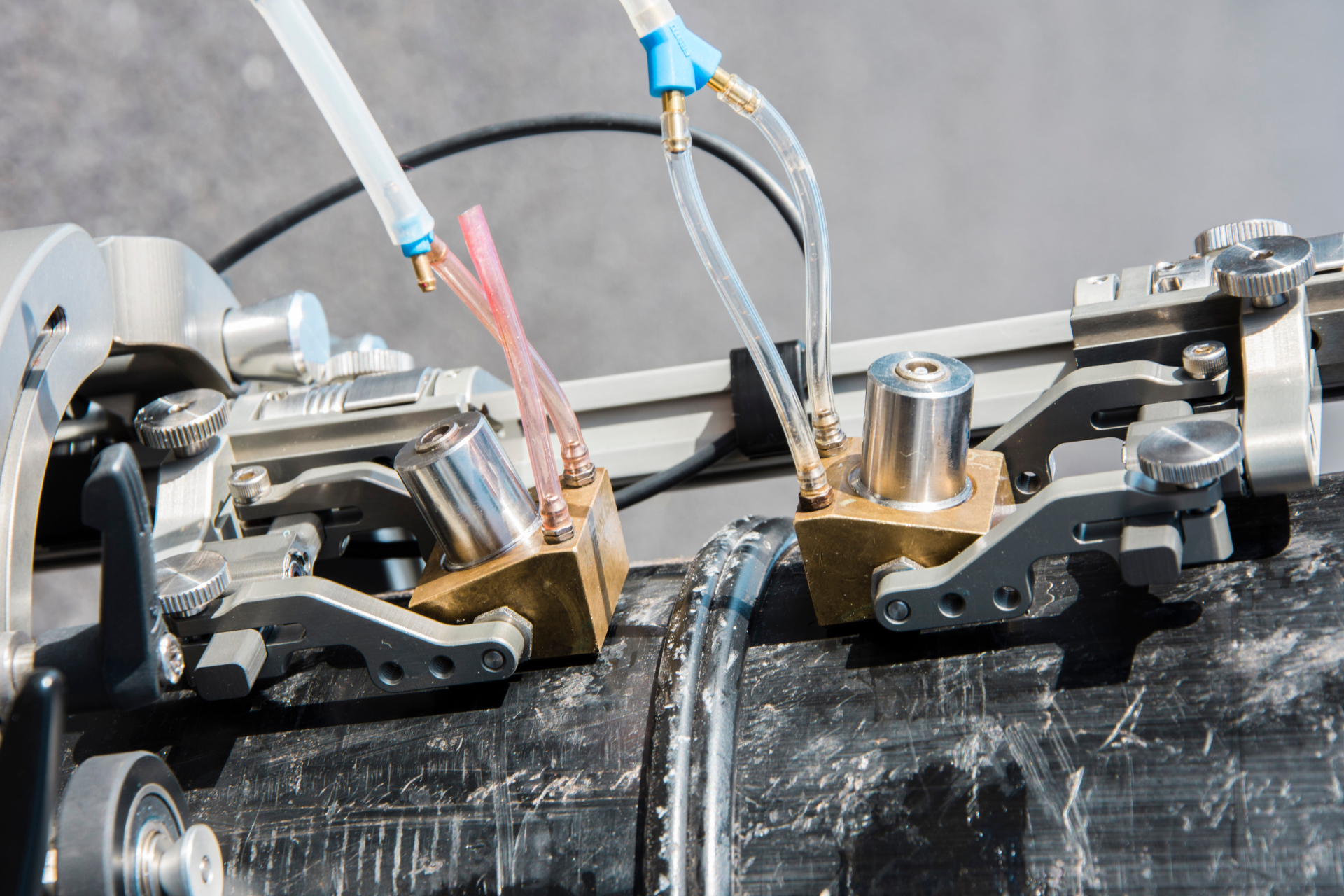
TFM is implemented by applying an algorithm to the full phased array data set collected by Full Matrix Capture [FMC].
The information collected from this advanced testing method is not summarised rather it is broken down to a granular level. Each transmitter/receiver from the probe’s array has its result digitised. Then, the algorithm calculates the focal law for each pixel. This process is much more detailed than the single assumed focal law and a summarised signal. As a result, it provides a thorough picture of the part under inspection.
The first step in applying the Total Focusing Method is to define the grid of focusing points. The data obtained from each transmitter/receiver combination is summed for each particular focusing point on the grid. The image is therefore constructed using the maximum amount of information available for each point. The image is a colour-coded display of the amplitudes produced after the application of the TFM algorithm.
There are several advantages of TFM that include but are not limited to:
- Optimal focusing and spatial resolution everywhere.
- Direct imaging of a large area for one probe position.
- All reachable angles with the array simultaneously.
- Defect characterisation.
- Comprehensive imaging of defect.
- 3D imaging.
While the benefits of TFM – FMC data collection are evident, there are still some drawbacks to the technique:
- quite large data files
- slow scanning speeds
- reduced signal-to-noise ratios [SNR] since the data is collected after pulsing just one element at a time
- same focalisation issues as regular PAUT inspection, thus a compromise may be required to find the most effective solution.
Similar to PAUT and further, in combination with fast electronics, computer technology and image processing, TFM now enables tomographic imaging in real-time even in austenitic weld seams that are considered examples of anisotropic materials, which can be examined with this method.Ηowever, it is still not believed to be effective for anisotropic materials such as modern TMCP pipeline steels as the algorithms rely on the assumption of isotropic material velocity.
Utilising TFM can help technicians identify small defects or flaws in challenging inspections. While standard PAUT remains the method of code and regulation, TFM can still help companies improve safety and maintenance results. Some case studies in the Oil and Gas industries -where it is common to face dissimilar metal welds, with complex geometries, multiple acoustic interfaces, and austenitic structure propagation issues- can be solved with TFM.
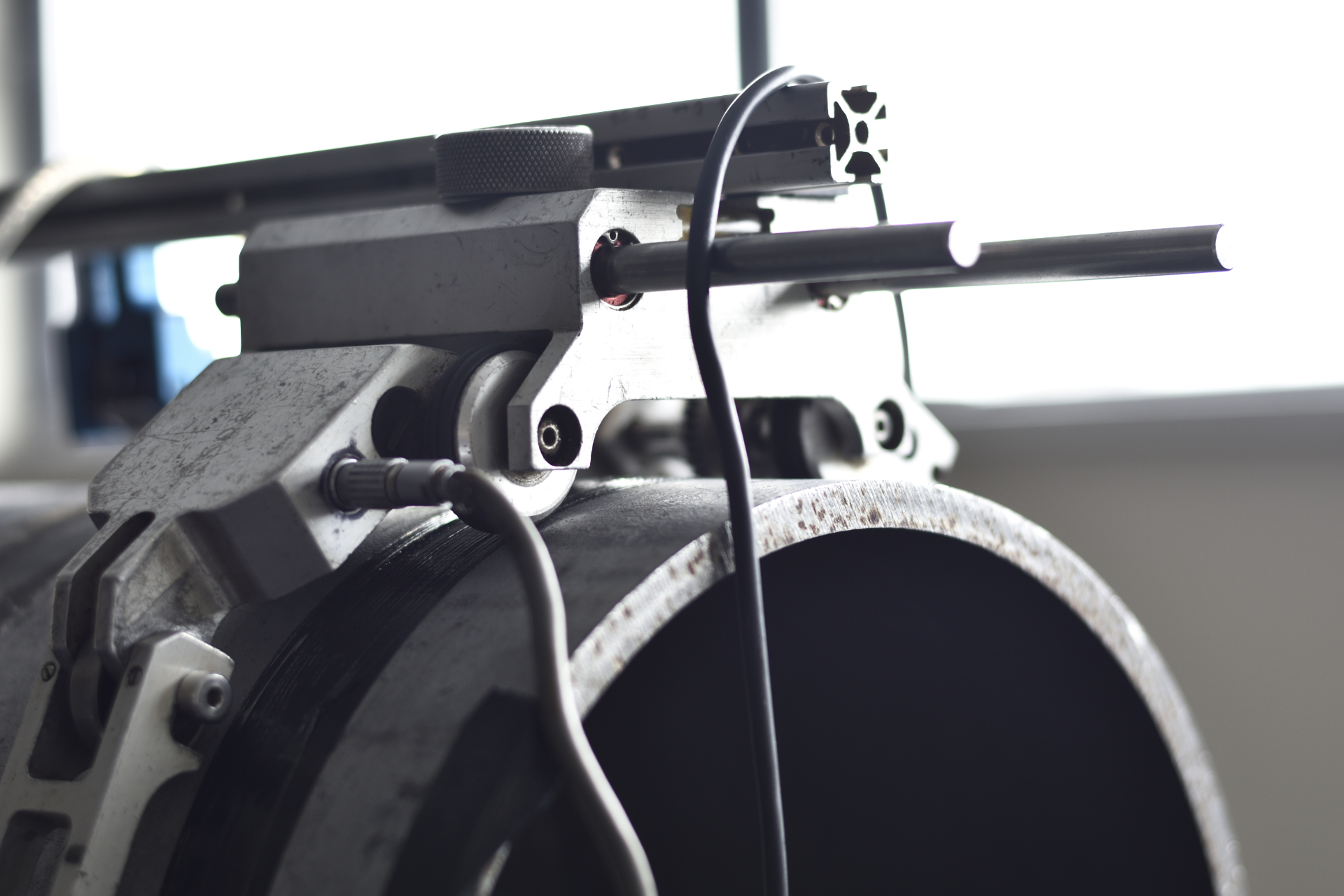
Newtron TFM testing can be used to assess a wide array of assets as this is becoming increasingly used across all engineering sectors including oil & gas and power generation.
TFM is very much an ‘evolving technology’. There are various working groups looking at it, but there is still only very limited agreement about the way they should go. ISO 23865 “Non-destructive testing — Ultrasonic testing — General use of full matrix capture/total focusing technique (FMC/TFM) and related technologies (2021)” gives general provisions for applying ultrasonic testing with arrays using FMC/TFM techniques and related technologies. It is intended to promote the adoption of good practice either at the manufacturing stage or for in-service testing of existing installations or for repairs.
This information is a collection of references. While we have made every attempt to ensure that information on this site is updated, Newtron is not responsible for any errors or omissions, or for the results obtained from the use of this information. It is not guaranteed to be complete, correct, current, or up to date and may be changed without prior notice.